Bronze sculptures and lost wax casting
Bronze is one of the most popular materials for making sculptures or plastic objects.
Its use must be traced back to the historical period in which the metallurgical practice of bronze was established and spread, which was called, precisely, the Bronze Age.
Widely used in the production of work or hunting tools, this alloy was not only used for functional reasons. Right from the start its work was also established for the production of furnishings and jewelry, but also of statues.
In the sculptural representation, bronze saw its main development in Greek art: if it was already
in the archaic period, it was in the classical one that the processing was refined and brought to its greatest expressiveness.
One of the best known examples are the famous Riace Bronzes.
Found in the Ionian Sea 300 meters from the Riace coast, they are now preserved in the National Museum of Reggio Calabria. The two sculptures were made with the lost wax casting technique, handed down over the years and also used in the following centuries, up to the present day.
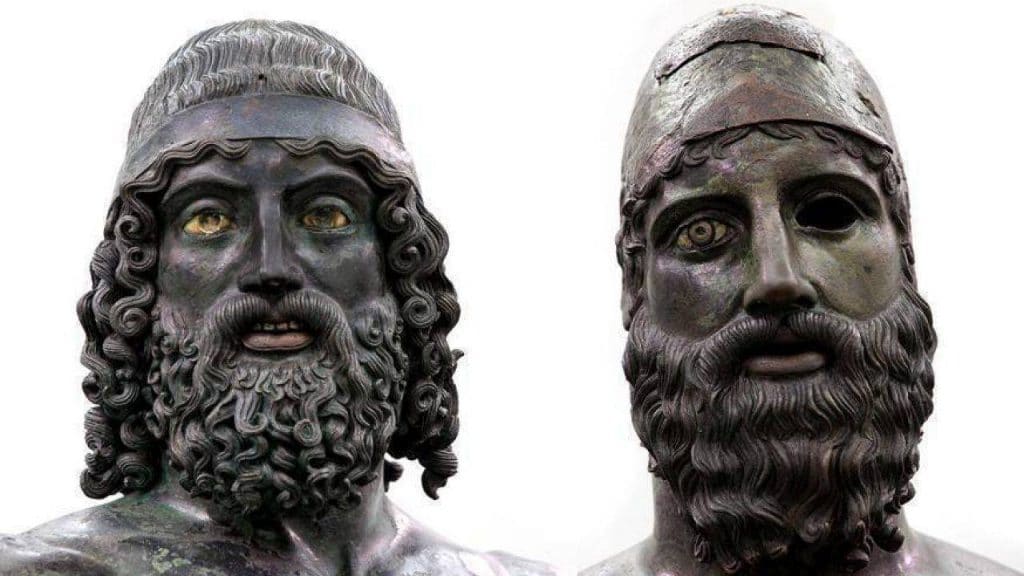
Many artists chose this technique, including Leonardo da Vinci for the famous equestrian monument to Francesco Sforza, unfortunately never built, but reached us through the conspicuous graphic apparatus produced by the artist in the design phase.
The bronze technique was widely used in sculptural production due to the great plastic possibilities, but also for intervention and modification during the design.
Last but not least, certainly a fundamental factor, was the relative ease with which bronze could be found. Reused material par excellence, it was often obtained from the fusion of older sculptures or ornamental parts. In this regard, the reuse of the bronze joints of the beams of the Pantheon, merged at the behest of Pope Urban VIII Barberini and reused to make the cannons for Castel Sant’Angelo, was well known. The criticisms were such that the pope was forced to declare that most of the material would have been used for the construction of the canopy of St. use of a scarce league by the Romans.
From a technical point of view, the bronze sculptures were mainly made, as already mentioned, with the personal wax techniquea.
The procedures could be of two different types, with direct method and indirect method, leading respectively to the creation of a solid sculpture and a hollow. The first method involved a lower number of steps, certainly more immediate, but could be applied to works of limited size, for which being of solid bronze would not have particularly affected the weight.
The indirect technique implied greater complexity, but was characterized as a necessary choice for works of considerable size. Several hollow pieces could be obtained, more easily handled and transportable, subsequently assembled to obtain final sculptures even of large dimensions.
The direct method involved the creation of a wax model, subsequently covered with clay, in order to create a mold. It was therefore heated and the wax came out through the slides, small tubes made of clay, into which the molten bronze was subsequently poured. The mold was therefore eliminated, obtaining a sculpture completely identical to the initial wax model.
The indirect method was very similar, but the starting model was in clay, on top of which the wax one was finished, with dimensions and proportions identical to those that were to be obtained in the finished work. The shape thus obtained was covered with clay, also equipped with slides through which the heated wax was made to flow out and replaced by the molten metal.
The possibility of intervening in the design phase was precisely given by the simplicity of processing the wax. easily malleable plastic material, it made it possible to modify by adding or removing material. Often the wax model also served as a preparatory to be submitted to the approval of the clients, before proceeding with further modifications and with the final casting.
There is actually a third procedure, ground fusion, which has spread mainly due to the potential capacity for unlimited reproduction starting from the reference model and the smaller reduction of the measurements from the original model, compared to previous techniques. The ground casting, however, led to the creation of a product generally of lower quality and usually of small dimensions or in any case of works that can be extracted in a single piece and therefore do not have excessive undercuts. For this reason this procedure was used above all for bas-reliefs, medals or plaques. In fact, it provided for the use of brackets, sort of boxes without a bottom, which could be stacked on top of each other according to the size of the object to be made. Therefore, molds were made starting from models that were pressed on the refractory earth, thus leaving their own cast. In this mold the bronze was then cast to obtain the finished work, which was finished only in the visible part, while the rear one was left rough.
In all three procedures, however, once the sculpture had cooled, it was not yet ready. In fact, all the tubes that marked the dripping and all those imperfections generated by small defects in the casting had to be removed.
In fact, the artist had to finish the work with small retouches and finally polish it, to obtain a good result. This phase often also involved further decoration of the surface through a process called chiseling. This consisted of a real work as a stonemason, making use of the use of burin and hammer, to engrave the bronze, drawing various and refined motifs that adorned the sculpture, for example in the backgrounds or to emulate the fabrics. The figure of the engraver was fundamental, especially in the various reproductions starting from an initial model. In fact, the revival of identical bronze sculptures derived from a reference prototype was quite widespread, especially if it was famous and highly appreciated.
If the copies are recognizable even for slightly smaller sizes compared to the original, due to the process of reproduction with the molds, it was the intervention of the engraver that strongly influenced the finished product. His ability to decorate and refine the work in fact strongly influenced its quality and, therefore, also its value.
Further difficulty existed where the various pieces needed to be assembled together. In this regard, the design phase was already fundamental, during which the modeler had to foresee the locking method between the pieces, but above all the interlocking. This passage was all the more difficult if we consider that, once the casting had taken place, the bronze sculpture did not allow the addition of material and that the bronze undergoes a shrinkage during the cooling phase, to a greater extent if it is a solid piece.
Different methods based on the refinement of the final work and its destination, bronze casting has always been applied in artistic production. From large sculptures to applications to enrich furniture, even the practice of making and finishing has remained almost constant over the centuries.
Procedure to which bronze was often subjected, to embellish objects made of this material was gilding. It is not unusual, in fact, to find details of large sculptures or entire small gilded bronzes, or even bronze applications on gilded furnishings, to play on the different lighting effects between wood and metal.
Even the gilding could be carried out in different ways, based on the chronological period and the needs, but for this further information, see another article.
Below are two examples of bronze sculptures present in our gallery.